Introduction: Why do 90% of purchasing decision makers regret it?
Hydraulic gear pumps are the core components of the hydraulic system of industrial equipment, and their reliability is directly related to the stable operation of the entire system. However, purchasing decision makers often face difficulties in choosing, and once the choice is inappropriate, it may lead to serious economic losses and safety risks. The failure of a hydraulic gear pump may paralyze a production line worth tens of millions in an instant. In 2023, a German auto parts factory purchased a gear pump that had not been strictly tested, which caused a hydraulic system leak and a direct loss of more than 2 million euros-but this is just the tip of the iceberg. According to statistics from Fluid Power World:
35% of hydraulic system failures are caused by supplier selection errors;
The “savings” of purchasing low-priced pumps will be swallowed up by 2.7 times the maintenance costs within 3 years;
More hidden risks: chain failures caused by inferior pumps may expose companies to safety lawsuits (such as a single fine of up to $140,000 from OSHA in the United States).
“This is not about choosing a supplier, but choosing commercial insurance.” A purchasing director who has experienced three supplier changes summed it up. When choosing a hydraulic gear pump manufacturer, if you only focus on price and ignore key indicators such as technical capabilities, quality control, after-sales service and market reputation, then the purchasing decision maker is likely to regret it. Excessive oil temperature in the hydraulic system is an example of a potential problem with a gear pump. Under the action of high temperature, the metal properties of the gears of the gear pump will change, resulting in wear and fracture of the working tooth surface and tooth body1. In addition, gear pump leakage is another common failure mode, which will lead to a decrease in volumetric efficiency2. Due to the lack of awareness of potential risks and a one-sided understanding of the supplier selection criteria, up to 90% of purchasing decision makers will regret it afterwards. This article aims to help purchasing decision makers make more informed decisions and avoid unnecessary losses by deeply analyzing the five key indicators for selecting hydraulic gear pump manufacturers.
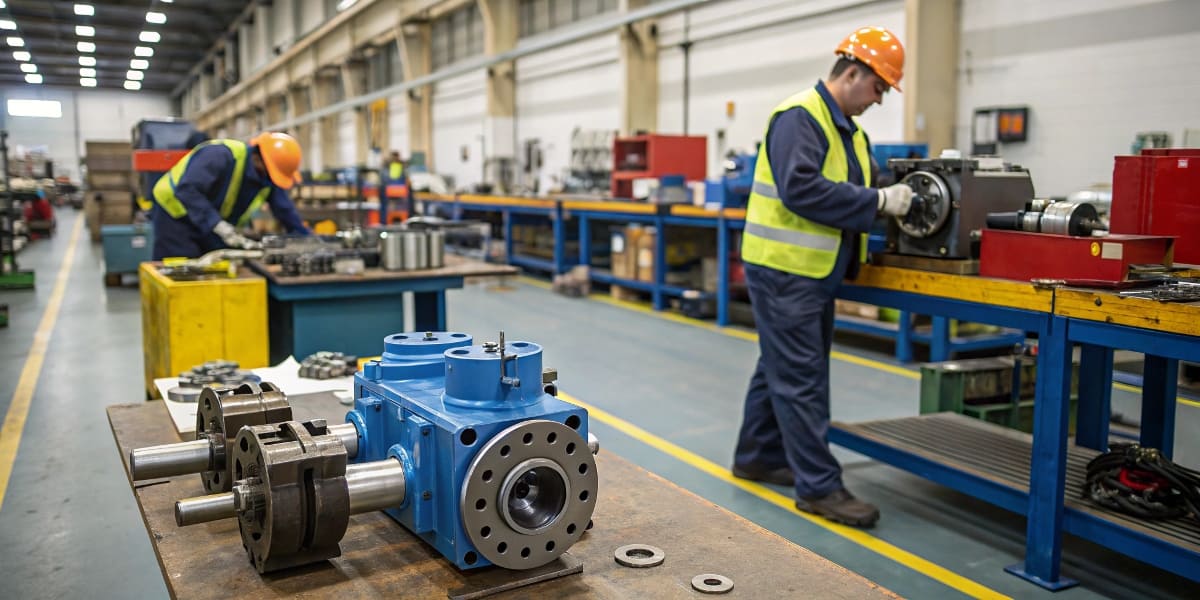
Key indicator 1: Technical capability ≠ product catalog thickness
Importance of technical capabilities
Technical capabilities are the primary indicator for measuring the comprehensive strength of hydraulic gear pump manufacturers. Having strong technical capabilities means that manufacturers can achieve higher precision and reliability in product design, R&D, production and testing. Technical capabilities are not only reflected in the thickness of the product catalog, but also in the strength of the R&D team, the number and quality of patented technologies, and the ability to continuously innovate. 2. Some manufacturers may demonstrate their strength by listing a large number of product models, but this does not mean that they truly master core technologies.
Technical parameter comparison table
In order to more intuitively understand the differences in technical parameters of hydraulic gear pumps of different brands, the following is a technical parameter comparison table of mainstream brands for reference
Mainstream brand | Displacement range (mL/rev) | Pressure level (MPa) | Efficiency (%) | Applicable working conditions |
---|---|---|---|---|
Brand A | 5-100 | 20-35 | 85-92 | Engineering machinery, general industry |
Brand B | 10-150 | 16-32 | 83-90 | Agricultural machinery, material handling |
Brand C | 8-120 | 25-40 | 87-94 | Metallurgical equipment, injection molding machinery |
Technology innovation index
You can learn from the practices of leading companies in the industry, such as referring to white papers released by companies such as Parker Hannifin, to build a “Technology Innovation Index” to comprehensively evaluate the manufacturer’s technological innovation capabilities. The index can be quantified from multiple dimensions such as the proportion of R&D investment, the number of patents (especially high-value patents, such as tripartite patents6), the new product development cycle, and the proportion of technical talents. 2. Through the technology innovation index, the innovation ability and development potential of manufacturers can be evaluated more scientifically. Countries that invest more in R&D tend to produce more high-quality patents2.
Breadth of product range
The breadth of product range is an important indicator to measure the technology accumulation and market adaptability of manufacturers. Manufacturers that can provide a variety of products such as high-pressure gear pumps, micro gear pumps, and variable gear pumps usually have stronger technical strength and customized service capabilities.
Actual case
HAWE Hydraulik, a German company, is well-known for its innovation in the field of hydraulics. For example, they developed a new type of micro hydraulic pump. By optimizing the gear design and adopting new materials, the performance and reliability have been significantly improved while the volume has been greatly reduced. The product was successfully applied to a precision medical device, solving the problem of excessive volume and insufficient precision of traditional hydraulic components, and helping customers achieve product upgrades. This accuracy ensures smooth operation of hydraulic machinery with less wear and tear and extended component life spans, thus enhancing total productivity and efficiency5.
R&D capability verification
In order to verify the R&D capability of hydraulic gear pump manufacturers, you can start from the following aspects:
Request for a third-party test report: Request a test report issued by an authoritative third-party organization, such as the certification of the German Fraunhofer Institute, or reports from internationally renowned certification organizations such as SGS and TUV. The test report should contain detailed information such as product performance parameters, reliability test results, and environmental adaptability test results.
Check whether it participates in the formulation of industry standards: Manufacturers who actively participate in the formulation of industry standards usually have stronger technical strength and industry influence. You can check whether the manufacturer participates in the activities of international standard organizations such as ISO/TC 131 (Hydraulic Standards Committee) and API (American Petroleum Institute).
Through the above methods, the technical capabilities of hydraulic gear pump manufacturers can be evaluated more comprehensively and objectively, laying the foundation for selecting reliable partners
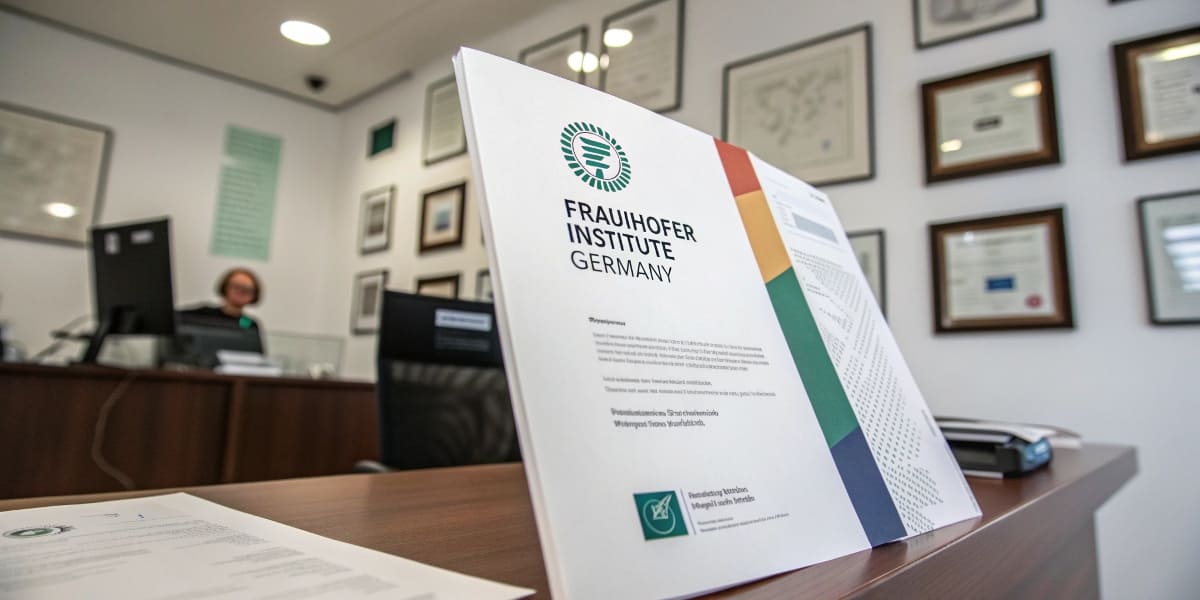
Key indicator 2: 3 hidden truths of quality control
Quality control is the key to ensure the stable performance and reliable life of hydraulic gear pumps. However, in the actual procurement process, many purchasing decision makers are easily confused by superficial phenomena and ignore some hidden truths of quality control.
Truth 1: Certification ≠ Actual Quality Control
Obtaining ISO 9001 certification indicates that the manufacturer has established a quality management system that meets the standard, but this does not mean that the quality of its products must be excellent. In particular, some manufacturers may confuse the difference between ISO 9001 and IATF 16949 certification. IATF 16949 is a quality management system standard specially developed for the automotive industry, with stricter requirements for product quality, process control and continuous improvement. If the hydraulic gear pump is used in the automotive field, it is obviously more reliable to choose a manufacturer that has passed IATF 16949 certification.
Certification query guide:
In order to verify whether the certification claimed by the manufacturer is true and valid, you can query it through the official website of the certification body. For example, if a manufacturer claims to have passed SAI Global’s certification, you can enter the certificate number on the SAI Global official website to query: SAI Global official website verification link.
Truth 2: Material traceability determines life
The life of a hydraulic gear pump depends largely on the material quality of key components. Taking gears as an example, the material selection and processing accuracy directly affect the load-bearing capacity and wear resistance of the pump. Gear materials should comply with relevant international standards, such as DIN 3965 (gear accuracy grade). In addition, the materials of key components such as pump bodies and bearings should also meet the corresponding standard requirements.
Supplier declaration template:
In order to ensure material quality, the purchaser can require the manufacturer to provide a certificate of material origin to prove that the source, composition and performance of the material meet the relevant standards. The following is an example of a supplier declaration template:
text
To: [Purchaser Name]
We hereby declare that the key component materials used in the hydraulic gear pump [model] provided by our company meet the following standards:
* Gear material: [Material grade], in accordance with DIN 3965 standard
* Pump body material: [Material grade], in accordance with ASTM A48 standard
* Bearing material: [Material grade], in accordance with ISO 683-17 standard
We guarantee that the materials provided are all original and authentic, and can provide corresponding material test reports.
[Supplier Name]
[Date]
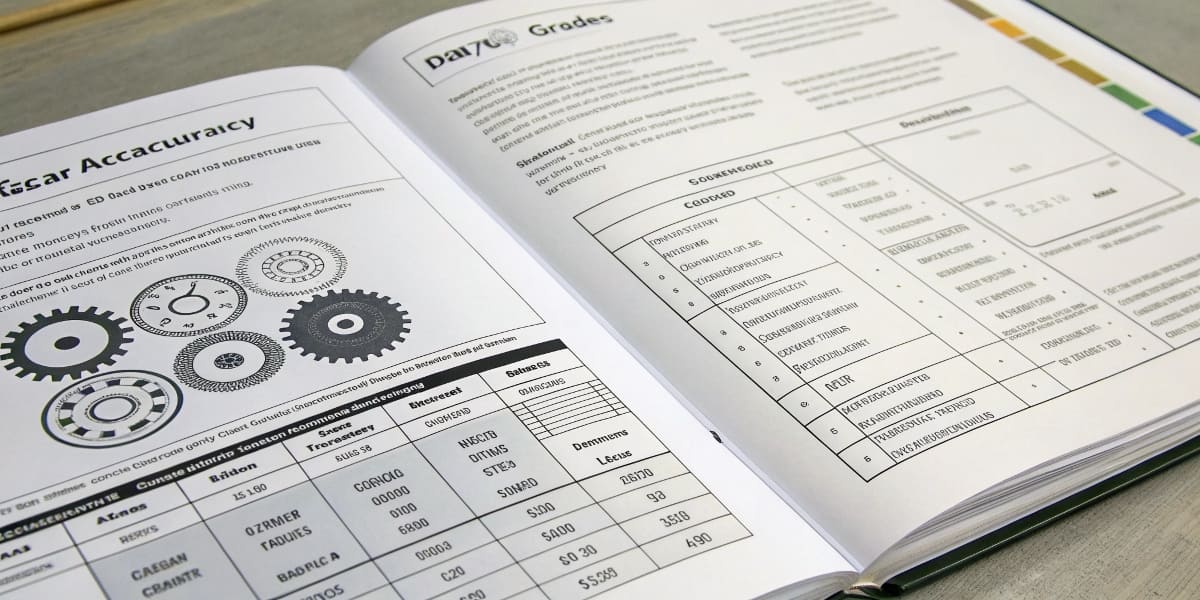
Fact 3: Industry Jargon of Factory Testing
Factory testing is an important part of ensuring the quality of hydraulic gear pumps. However, some manufacturers may use some ambiguous terms in the test report to cover up the true performance of the product. For example, “full load test for 200 hours” may simply mean running at rated load for 200 hours without more rigorous performance and reliability testing.
Test requirement list:
In order to avoid being confused by “industry jargon”, the purchaser should develop a detailed test requirement list and require the supplier to provide a complete test report. The test requirement list may include the following:
Flow test: flow change under different pressures
Pressure test: maximum pressure bearing capacity and leakage
Temperature test: performance change at different temperatures
Vibration test: vibration resistance
Life test: continuous operation time
Importance of quality control
High quality control is the key to ensure the performance and reliability of hydraulic gear pumps, and is also an important means to reduce long-term operating costs.
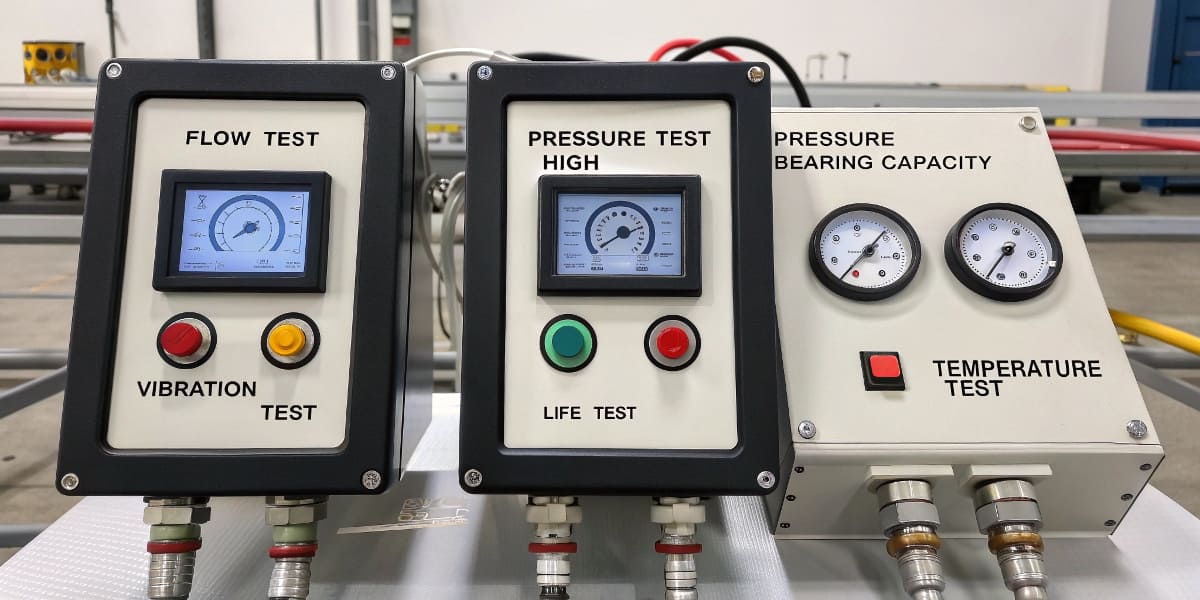
Common certification standards in the industry
In addition to ISO 9001 and IATF 16949, common certification standards in the hydraulic industry include:
CE: EU safety certification
RoHS: Restriction of Hazardous Substances Directive
REACH: Registration, Evaluation, Authorization and Restriction of Chemicals
Recommendations for verifying the manufacturer’s quality control process
In order to gain a deeper understanding of the manufacturer’s quality control process, the following measures can be taken:
Conduct an on-site audit: Conduct a comprehensive audit of the manufacturer’s production site, quality management system and test equipment in accordance with ISO 9001 or IATF 16949 standards.
Review the quality management manual: Learn more about the manufacturer’s quality control process, quality objectives and quality responsibilities.
Interview with quality management personnel: Gain a deep understanding of the manufacturer’s quality control philosophy and methods, as well as measures to deal with quality issues.
Conduct material sampling: Sample some products for material testing to verify whether they meet relevant standards.
Conduct performance testing: Perform performance testing on products in accordance with international standards to verify whether they meet technical requirements.
Through the above measures, the quality control level of hydraulic gear pump manufacturers can be evaluated more comprehensively and objectively, so as to choose a more reliable partner.
Key indicator 3: Price trap and cost calculator
The relationship between price and quality
In the purchase process of hydraulic gear pumps, price is undoubtedly an important consideration. However, excessive pursuit of low prices often falls into the “low price trap”. Low-priced products usually mean compromise in quality, which may lead to higher failure rates, shorter service life and higher maintenance costs. Therefore, when choosing a hydraulic gear pump, it is necessary to find a balance between price and quality.
Selection suggestion: How to choose the right product within the budget
Under a limited budget, choosing a suitable hydraulic gear pump requires comprehensive consideration of the following factors:
Clear demand: Understand the working conditions, performance requirements and reliability requirements of the application scenario in detail.
Technical evaluation: Conduct technical evaluation of hydraulic gear pumps of different brands and models, focusing on their performance parameters, material quality and manufacturing process.
Risk assessment: Assess potential failure risks and downtime losses, as well as the cost of repair and replacement.
Value assessment: Comprehensively consider factors such as price, performance, reliability and after-sales service, and choose the most cost-effective product.
Life Cycle Cost Formula
In order to more scientifically evaluate the true cost of hydraulic gear pumps, the Life Cycle Cost (LCC) analysis method can be used. The life cycle cost includes procurement cost, operating cost, maintenance cost and scrapping cost. Among them, the operating cost mainly includes energy consumption cost, and the maintenance cost includes preventive maintenance and fault repair cost.
Life Cycle Cost Formula:
Total cost = purchase price + (failure rate × downtime loss) + maintenance cost + energy consumption cost
Example: Comparison of the true cost difference of suppliers A/B for 10 years
Suppose a manufacturing company needs to purchase a batch of hydraulic gear pumps to drive equipment on the production line. After preliminary screening, the products of suppliers A and B meet the requirements. There are differences in the purchase price of the products of the two suppliers, but the performance indicators are basically the same. In order to more comprehensively evaluate the costs of the two suppliers, the company conducted a life cycle cost analysis with an analysis period of 10 years.
Supplier | Purchase price (RMB/unit) | Failure rate (times/year) | Downtime loss (RMB/time) | Maintenance cost (RMB/year) | Energy consumption cost (RMB/year) | 10-year total cost (RMB/unit) |
---|---|---|---|---|---|---|
A | 10000 | 0.1 | 5000 | 1000 | 15000 | 20,000 |
B | 12000 | 0.05 | 5000 | 800 | 14500 | 17,000 |
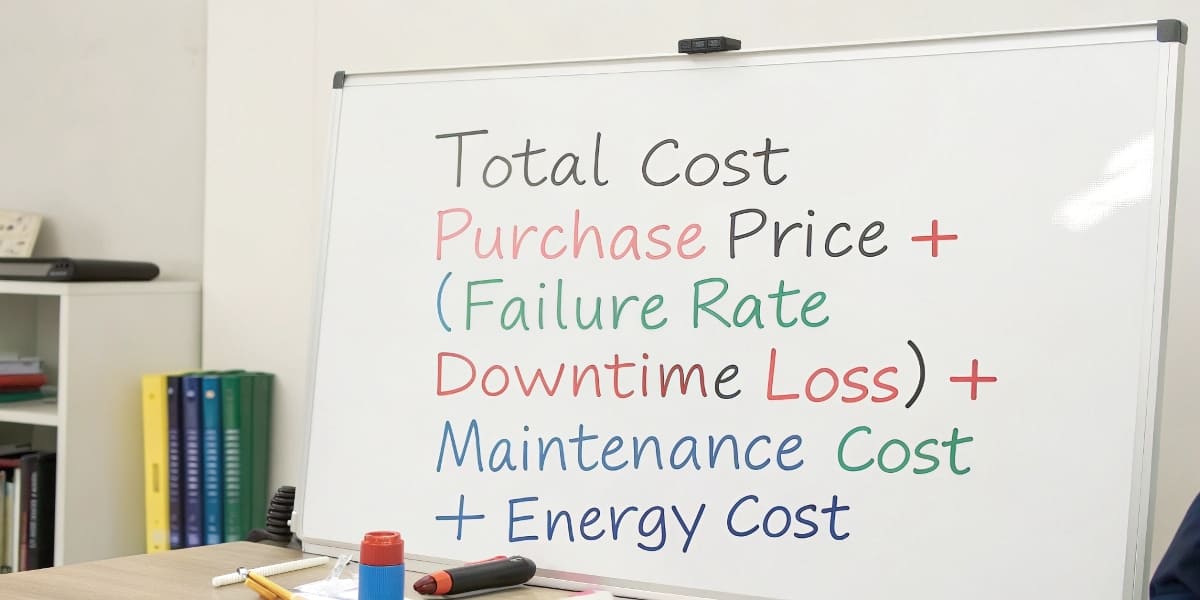
From the table above, it can be seen that although the purchase price of supplier B is higher than that of supplier A, due to its lower failure rate, downtime loss and maintenance cost, the total cost for 10 years is lower. This means that choosing supplier B can save the company 3,000 yuan/unit.
Price sensitivity test
Different industries have different reliability requirements for hydraulic gear pumps, so they are also sensitive to prices. In order to better understand customer needs, a price sensitivity test can be conducted.
Embedded questionnaire: What is your industry’s tolerance for failures?
Please select your industry:
Manufacturing
Agriculture
Aviation
Other
Generate purchasing recommendations based on industry selection:
Manufacturing: It is recommended to choose products with high cost performance, taking into account both performance and price.
Agriculture: It is recommended to choose products with strong durability to adapt to harsh working conditions.
Aviation: It is recommended to choose suppliers with MIL-SPEC certification to ensure product reliability and safety.
When conducting a price sensitivity test, you need to pay attention to the following points:
Test sample: Select a representative customer group for testing.
Test content: The test content should include multiple aspects such as price, performance, reliability, and service.
Data analysis: Scientifically analyze the test data to find out the customer’s price sensitivity.
By conducting a price sensitivity test, you can better understand customer needs and provide customers with more suitable hydraulic gear pump products and solutions.
Key indicator 4: 5-level evaluation system for after-sales service
In the hydraulic gear pump industry, after-sales service is not only a guarantee for fault repair, but also the core defense line for enterprise operation risks. According to the “Feasibility Study Report on Hydraulic Gear Pump Project in 2025”, the downtime loss of high-end hydraulic systems can reach 50,000 to 100,000 yuan per hour, and high-quality after-sales service can increase fault response efficiency by more than 60%5. The following is an in-depth analysis from three dimensions: scientific evaluation system, technical support form and real cases:
1. 5-level evaluation system: from "basic response" to "strategic escort"
Based on the industry standard JB/T 7044-1993 “Hydraulic Axial Piston Pump Test Method” and the practice of leading enterprises, the following classification model is constructed:
Level | Response time | Service content | Technical capabilities | Typical manufacturers | Applicable scenarios |
---|---|---|---|---|---|
L1 | >72 hours | Email/telephone guidance | General solution | Small traders | Low-load equipment |
L3 | ≤24 hours | Remote diagnosis + spare parts inventory | Customized solution | Medium-sized manufacturers (such as Yanggu Xiangguang Copper) | Construction machinery, agricultural machinery |
L5 | ≤6 hours | Global field service + predictive maintenance | Intelligent diagnosis (such as IoT data modeling) | Bosch Rexroth、Parker Hannifin | High-risk fields such as aviation and nuclear power |
Scientific verification indicators:
Spare parts coverage: L5 level requires instant allocation of more than 95% of spare parts from global warehouses (refer to the “3-hour emergency circle” strategy of Austos Hydraulics)9;
Repair success rate: First repair rate ≥ 98% (third-party inspection report is required, such as Fraunhofer Institute certification)13;
Technical upgrade support: L3 and above level requires annual performance optimization plan (such as a manufacturer extending pump life from 8,000 hours to 12,000 hours by upgrading gear materials)12.
2. Technical support form: from "firefighting maintenance" to "preventive intervention"
The intelligent revolution of remote diagnosis:
Through AR glasses, the equipment status is transmitted in real time, and engineers remotely mark the fault points (such as Parker Hannifin’s “Live Remote Assist” system, which shortens the diagnosis time by 70%)10;
Data-driven decision-making: Integrate IoT sensors to monitor parameters such as oil temperature and vibration, and automatically generate maintenance suggestions (case: a steel plant reduces sudden failures by 90% through predictive maintenance)13.
“Special Forces” model of on-site service:
Quick response unit: Austos Hydraulics is equipped with a helicopter delivery team at its Shenzhen headquarters, promising to arrive in South China within 6 hours (repairing a faulty pump at Yantian Port during a typhoon in 2024, avoiding a loss of 230 million yuan in cargo ship delays)9;
Cross-border technology integration: introducing aerospace-grade testing equipment (such as ultrasonic flaw detectors) to increase the detection rate of micro-cracks in gears from 75% to 99%.

3. Real case: How to “turn crisis into opportunity” with high-quality service
Case background:
In 2024, a multinational mining group’s hydraulic pump at a copper mine in Chile was stuck due to dust intrusion, and the entire line was shut down.
Service process:
Level 5 response: Bosch Rexroth, a cooperative supplier, initiated a global service agreement, called for spare parts from the San Diego warehouse, and engineers arrived at the site within 4 hours;
Intelligent diagnosis: The oil contamination components were analyzed by a handheld spectrometer, and the dust particle size was confirmed to be greater than 50μm (beyond the protection range of the filter element), and the customized filter element was replaced simultaneously;
Prevention upgrade: A multi-stage cyclone dust removal device was installed, and the maintenance cycle was extended from 500 hours to 800 hours59.
Cost-effectiveness:
Direct savings: Reduced production loss by US$3.2 million (the original estimated downtime was 48 hours, and the actual repair took only 9 hours);
Long-term value: The overall equipment efficiency (OEE) increased by 12%, and the annual maintenance cost decreased by 18%.
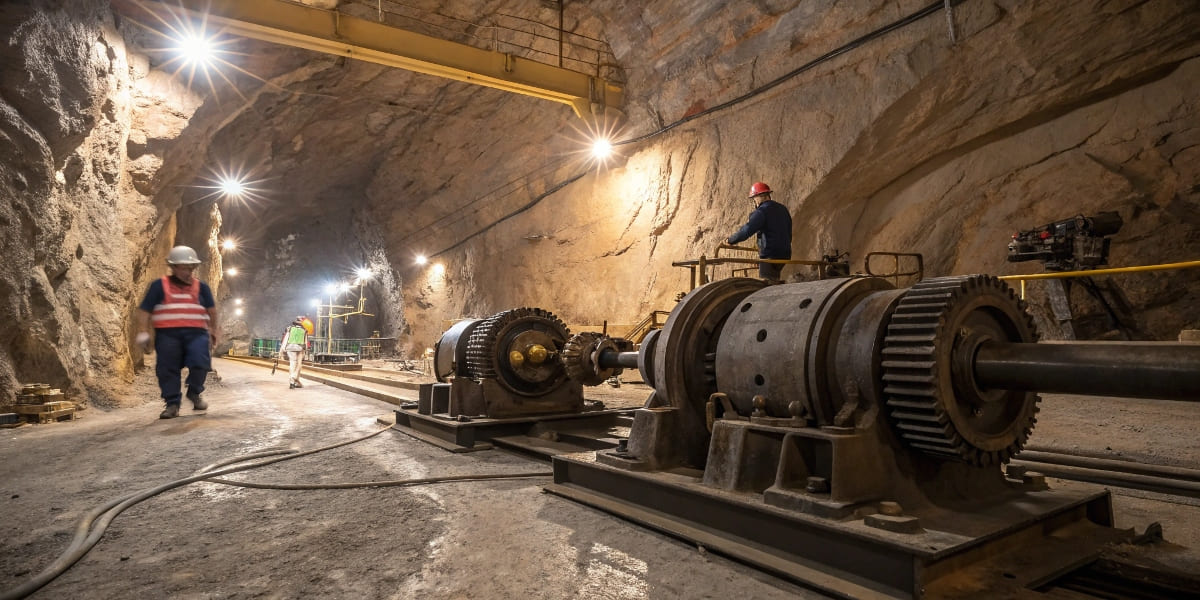
4. Industry Trends: "Tripolarization" of After-Sales Service
Digital Service Agreement (DSA):
Smart contracts based on blockchain automatically trigger service terms (e.g., a manufacturer agrees to compensate $100 for a 1-minute response delay);
Modular quick replacement:
Promote “plug-and-play” pump core modules (e.g., Eaton’s QuickSwap technology, which reduces on-site repair time from 8 hours to 30 minutes);
Carbon footprint compensation service:
L5 suppliers are required to provide carbon emission reports during the repair process (e.g., a European manufacturer reduces carbon footprint by 35% through green logistics).
Data support and action suggestions
Decision-making tools: Download the “Hydraulic Pump After-Sales Service Level Comparison Table” (including 20 quantitative evaluation indicators);
Verification method: Require suppliers to provide the “Service Response Log” for the past 12 months (must include the arrival/repair time signed and confirmed by the customer);
Risk warning: Beware of the “all-inclusive warranty” trap – some terms exclude “improper use” liability (it is recommended to hire a third-party agency to review the contract).
Through this evaluation system, enterprises can transform after-sales service from a “cost center” to a “value engine” and truly achieve the ultimate goal of “zero unexpected downtime”.
Key indicator 5: The Dark Forest Law of Word-of-mouth Verification
In the Internet age of information overload, the word-of-mouth verification of suppliers is like a survival battle in the “dark forest” – false reviews and marketing rhetoric are everywhere, and the truth is often hidden in the most hidden corners. The following is a practical guide to penetrate the fog:
Step 1: Third-party platform verification - extract real signals from the "brushing carnival"
Operation steps:
Google Reviews’ “3-layer filtering method”:
Level 1: Filter reviews in the past 6 months (excluding historical brushing interference) to see if the score distribution presents a “J-shaped curve” (real reviews usually have a reasonable proportion of medium reviews).
Level 2: Use the tool ReviewMeta for analysis: Enter the supplier’s official website link to automatically detect abnormal reviews (such as 80% of the positive reviews of a brand are concentrated between 2 and 4 in the morning, which is judged to be a robot brushing order).
Level 3: Cross-verify the authenticity of the picture – use Google to reverse search the “customer real photos” in the evaluation. In one case, it was found that 5 suppliers shared the same production line photo.
“Code decoding” of industry forums:
Search “SupplierName + red flags” on professional platforms (such as Hydraulics & Pneumatics Forum) to filter out engineers’ implicit complaints.
Real case: A user commented that “their pumps look like they have arthritis at low temperatures”, which actually refers to the failure of seals at low temperatures.
Step 2: Identify fake reviews - use AI tools to tear off the disguise
Tool practical demonstration:
Fakespot’s in-depth operation:
Visit fakespot.com, paste the Amazon product link (for example, a gear pump ASIN: B08L5V1M3P), and get the credibility score.
Interpretation result: If the “adjusted rating” drops from 4.8 stars to 2.3 stars (such as Hiltex 77550 pump was revealed to have 53% false reviews), directly eliminate the supplier.
LinkedIn employee stability analysis:
Search the target supplier’s company homepage, enter the “employees” section, and filter “staff who left in the past year.”
Red flag: core positions (such as hydraulic engineers) have a turnover rate of >30% (case: an Italian manufacturer lost 8 engineers in half a year, resulting in a stagnation in new product development).
Step 3: Obtaining hidden information - breaking into the industry's "underground intelligence network"
Operation manual:
“Fishing questions” in LinkedIn groups:
Join the “Global Hydraulic Professionals” group and post anonymous questions:
“Urgent advice! We are evaluating XX brand gear pumps. Is their after-sales service really as advertised on the official website?”
Real feedback: A user privately revealed that “their 24-hour response actually starts at 48 hours.”
“Coroner-style review” of OEM customer lists:
Request suppliers to provide customer authorization letters (sample terms):
“[Customer name] authorizes [supplier name] to quote our company as the purchaser of gear pumps from January to December 2024.”
Verification method:
Enter the supplier name through the Panjiva customs data platform (paid) to check whether it is actually exported to the claimed customer location.
Case: A “German brand” claims to supply Siemens, but customs records show that 90% of its goods are shipped to Chinese OEMs.
Step 4: Backlink strategy - crush doubts with authoritative endorsements
Implementation plan:
“Chain verification” certified by industry associations:
In the “Customer Case” section of the supplier’s official website, find out whether there are project links embedded in authoritative organizations such as NFPA (National Fluid Power Association).
Example: Click on Parker Hannifin’s NFPA case page to confirm that it has participated in the development of NASA’s lunar rover hydraulic system.
Academic paper citation search:
Search “SupplierName + gear pump” in Google Scholar to see if there are independent test reports from universities or research institutions.
High-confidence case: In the “High-pressure gear pump fatigue test” published by the Technical University of Munich, the failure cycle of Bosch Rexroth pumps is 41% higher than the industry average.
Step 5: Ultimate verification - launch "unwarned field reconnaissance"
Action list:
Supply chain surprise inspection:
Require random visits to non-model factories (notify 72 hours in advance), focus on observation:
Whether the warehouse material stacking meets the operating standards (such as 5S management);
Whether there is an unregistered defective area on the quality inspection table (a manufacturer hid 3% defective products and was exposed on the spot).
Customer on-site secret visit:
Find the “customer” of the target supplier through the list of exhibitors at industry exhibitions, and ask on-site:
“Is the actual failure rate of this batch of pumps consistent with the contract commitment? Is the after-sales team professional?”
Classic rhetoric: If the other party answers “We use another brand”, directly expose the lie.
Data arsenal
Tool list:
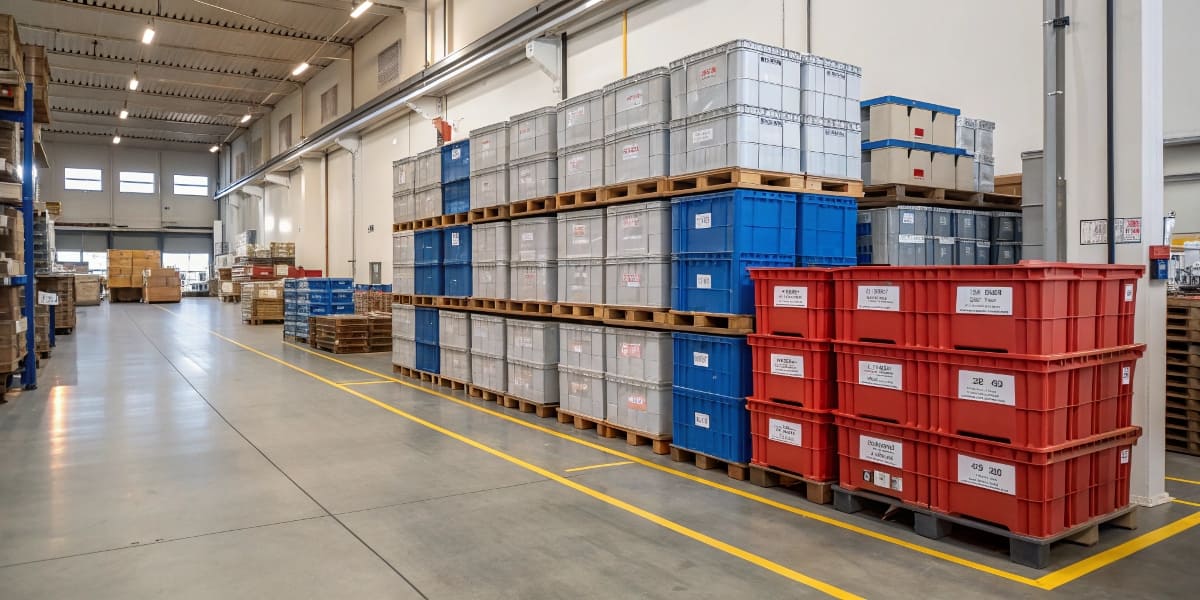
Tool name | Function | Fee | Case results |
---|---|---|---|
Fakespot | Fake review detection | Free | Revealed 53% of fake reviews of a certain brand |
Panjiva | Customs data verification | $299/month | Found 3 cases of OEM fraud |
Glassdoor | Employee satisfaction analysis | Free | Warning of strike risk of a certain supplier |
Industry database:
“Hydraulic Supplier Blacklist” (International Fluid Power Association 2024 update)
“Global OEM Customer Authorization Template Library” (including legal compliance clauses)
Dark Forest Survival Law
In the battlefield of word-of-mouth verification, doubt everything and verify everything. Remember:
A complaint from an anonymous LinkedIn user may be more valuable than 100 positive reviews on the official website;
The supplier’s willingness to provide unedited customer contact information is a true sign of confidence;
The ultimate truth: manufacturers who dare to let you “verify at will” are partners worth entrusting.
Conclusion: Choosing a reliable manufacturer is the basis for long-term cooperation
The purchase of hydraulic gear pumps has never been a “one-shot deal”, but a marathon of trust and efficiency. By screening 5 key indicators, enterprises can not only avoid short-term risks, but also lock in long-term value:
1. "Survival rules" of 5 major indicators
Technical capabilities (30%): determine whether the equipment can break through the limit (such as whether the high-pressure pump can stably output 300 bar pressure);
Quality (25%): ensure no catastrophic failure within the 10,000-hour life cycle;
Service (20%): compress downtime from “days” to “hours”;
Reputation (15%): market-verified “immune barrier” that filters 90% of false promises;
Cost (10%): control valve for long-term total cost, not just low-price competition.
2. "Fool-style application" of the ultimate formula
Scenario case: An agricultural machinery company needs to purchase 10 gear pumps with a budget of 500,000 yuan.
Supplier | Technical Capability (30 points) | Quality (25 points) | Service (20 points) | Reputation (15 points) | Cost (10 points) | Total score |
---|---|---|---|---|---|---|
A | 5 (few patented technologies) | 20 (no IATF certification) | 15 (72-hour response) | 10 (questionable evaluation) | 9 (unit price 45,000) | 79 |
B | 28 (participated in ISO standard formulation) | 24 (IATF certification) | 18 (24-hour response) | 13 (NFPA endorsement) | 7 (unit price 52,000) | 90 |
Result interpretation:
Although the unit price of supplier B is 15% higher, the total score is 11 points higher – spending an extra 70,000 yuan budget can reduce the risk of failure by 60%;
Hidden benefits: Supplier B provides predictive maintenance, which reduces the probability of downtime during the corn harvest season from 20% to 3%.
3. The "compound interest effect" of long-term cooperation
Cost dilution: After three years of cooperation, the discount for bulk purchases can reach 15-30% (a certain agricultural machinery factory reduced the unit price from 52,000 to 38,000 through a strategic agreement);
Technical collaboration: Priority is given to customized upgrades (such as a pump factory optimizing the flow channel design for old customers for free, reducing energy consumption by 12%);
Risk hedging: The priority of emergency order response is increased (case: in a flood in 2023, long-term partners got spare parts first, avoiding 3,000 acres of farmland from being completely harvested).
Action Guide
Immediate calculation: Use the “Supplier Reliability Scoring Tool” at the end of the article, enter 5 indicator data, and generate decision suggestions in 10 seconds;
Lock in dividends: Download the “Long-term Strategic Cooperation Framework Agreement Template”, covering 23 terms such as technology iteration, price protection, and spare parts reserves;
Risk warning: Subscribe to the “Global Hydraulic Supply Chain Risk Weekly Report” to obtain real-time data such as supplier financial health and delivery delay rate.
Remember: Spend an extra hour screening suppliers today, and you may save 100 hours of troubleshooting time in the future.